Introduction
In the industrial sector, a reliable source of power is essential to keep operations running smoothly. Diesel generators have long been a popular choice for providing backup power in industrial settings due to their robustness, efficiency, and reliability. In this article, we will explore the various aspects of diesel generators for industrial applications, including their working principle, advantages, applications, maintenance, and environmental impact.
Working Principle of Diesel Generators
Diesel generators operate on the principle of converting chemical energy stored in diesel fuel into mechanical energy through combustion. The basic components of a diesel generator include an engine, alternator, fuel system, cooling system, and exhaust system.
The engine is the heart of a diesel generator and is responsible for converting the chemical energy in diesel fuel into mechanical energy. It consists of a piston-cylinder arrangement where the air is compressed, and fuel is injected into the combustion chamber. The fuel-air mixture is then ignited by the heat of compression, resulting in the expansion of gases that drive the piston, producing mechanical energy.
The alternator, also known as the generator, is connected to the engine and converts the mechanical energy produced by the engine into electrical energy through the principle of electromagnetic induction. The electrical energy generated is then supplied to the industrial load to power various equipment and machinery.
The fuel system of a diesel generator is responsible for storing, filtering, and delivering the diesel fuel to the engine for combustion. A reliable fuel system is crucial for ensuring the uninterrupted operation of the generator.
The cooling system of a diesel generator helps regulate the temperature of the engine to prevent overheating and ensure optimal performance. It typically consists of a radiator, coolant, water pump, and fan to dissipate the heat generated during the combustion process.
The exhaust system of a diesel generator is designed to remove the combustion gases produced during the operation of the engine. It includes components such as the exhaust manifold, muffler, and exhaust pipe to direct the exhaust gases away from the generator and the surrounding environment.
Advantages of Diesel Generators for Industrial Applications
Diesel generators offer several advantages that make them well-suited for industrial applications:
1. Reliability: Diesel generators are known for their reliability and durability, making them ideal for providing backup power in industrial settings where downtime can result in significant financial losses. The robust design of diesel engines ensures continuous operation even under heavy load conditions.
2. Fuel efficiency: Diesel generators are more fuel-efficient compared to gasoline generators, as diesel fuel has a higher energy density, providing more power per unit of fuel. This makes diesel generators a cost-effective option for industrial applications where continuous power supply is essential.
3. Longevity: Diesel engines are designed to operate for extended periods without requiring frequent maintenance or overhauls. With proper care and maintenance, diesel generators can last for decades, providing a reliable source of backup power for industrial facilities.
4. Power output: Diesel generators are capable of generating high power outputs, making them suitable for powering heavy-duty equipment and machinery in industrial settings. They can handle sudden surges in power demand without compromising performance.
5. Easy availability of fuel: Diesel fuel is readily available in most parts of the world, making it convenient for industrial facilities to refuel their generators without any hassle. This ensures that the generator can be quickly refueled in case of an emergency or prolonged power outage.
Applications of Diesel Generators in Industrial Settings
Diesel generators find a wide range of applications in industrial settings, including:
1. Emergency backup power: One of the primary applications of diesel generators in industrial settings is to provide emergency backup power in case of grid power failure. Industrial facilities rely on diesel generators to ensure uninterrupted operation of critical equipment and processes during power outages.
2. Prime power supply: Diesel generators are also used as a primary source of power in remote industrial sites where grid power is unavailable or unreliable. They serve as the main power source for running machinery, lighting, heating, and other essential operations in such locations.
3. Peak shaving: Diesel generators are often used in industrial settings to reduce peak demand charges by supplementing grid power during periods of high electricity consumption. By operating diesel generators during peak demand hours, industrial facilities can lower their overall energy costs.
4. Standby power for critical loads: In industries where the loss of power can have severe consequences, such as data centers, hospitals, and manufacturing plants, diesel generators are employed to provide standby power for critical loads. These generators ensure that essential equipment remains operational during power outages.
5. Construction sites: Diesel generators are commonly used in construction sites to power tools, lighting, and other equipment where grid power is unavailable. Their portability and reliability make them an ideal power source for temporary power needs in construction projects.
Maintenance of Diesel Generators
Proper maintenance is crucial to ensure the reliable operation of diesel generators in industrial settings. Regular maintenance tasks include:
1. Fuel system maintenance: The fuel system of a diesel generator should be inspected and maintained regularly to ensure the proper storage, filtration, and delivery of diesel fuel. This includes checking for fuel leaks, changing fuel filters, and monitoring fuel quality to prevent issues such as clogging and contamination.
2. Cooling system maintenance: The cooling system of a diesel generator should be inspected for leaks, blockages, and proper coolant levels. Regular cleaning of the radiator and checking the water pump for proper operation are essential to prevent overheating and ensure optimal engine performance.
3. Engine maintenance: Regular engine maintenance tasks include checking oil levels, changing oil filters, inspecting belts and hoses, and monitoring engine performance. Proper lubrication of engine components is crucial to reduce friction and wear, prolonging the lifespan of the generator.
4. bojinsi : Diesel generators rely on batteries to start the engine and power essential control systems. Regular inspection of the batteries, cleaning of terminals, and testing of voltage levels are necessary to ensure the reliable operation of the generator during startup.
5. Exhaust system maintenance: The exhaust system of a diesel generator should be inspected for leaks, corrosion, and proper ventilation to prevent the buildup of toxic gases. Regular cleaning of the exhaust components and inspection of the muffler are essential for safe and efficient operation.
Environmental Impact of Diesel Generators
While diesel generators offer several advantages for industrial applications, they also have environmental implications that need to be considered:
1. Air pollution: Diesel generators emit pollutants such as nitrogen oxides (NOx), particulate matter (PM), and sulfur dioxide (SO2) during combustion, contributing to air pollution. These pollutants can have detrimental effects on human health and the environment, especially in densely populated areas.
2. Carbon footprint: Diesel generators are a significant source of greenhouse gas emissions, primarily carbon dioxide (CO2), which contributes to climate change. The combustion of diesel fuel releases CO2 into the atmosphere, leading to global warming and environmental degradation.
3. Noise pollution: Diesel generators are known for their noise emissions, which can be disruptive to the surrounding environment and communities. Noise pollution from generator operation can impact the quality of life for nearby residents and workers, especially in industrial areas.
4. Spill hazards: Diesel fuel storage and handling pose the risk of spills and leaks, which can contaminate soil, water sources, and ecosystems. Proper spill containment measures and regular inspections are necessary to prevent environmental damage from fuel spills.
5. Regulatory compliance: Industrial facilities using diesel generators must comply with environmental regulations and emission standards to minimize their impact on the environment. Regular emissions testing, maintenance of pollution control devices, and proper disposal of waste are essential for meeting regulatory requirements.
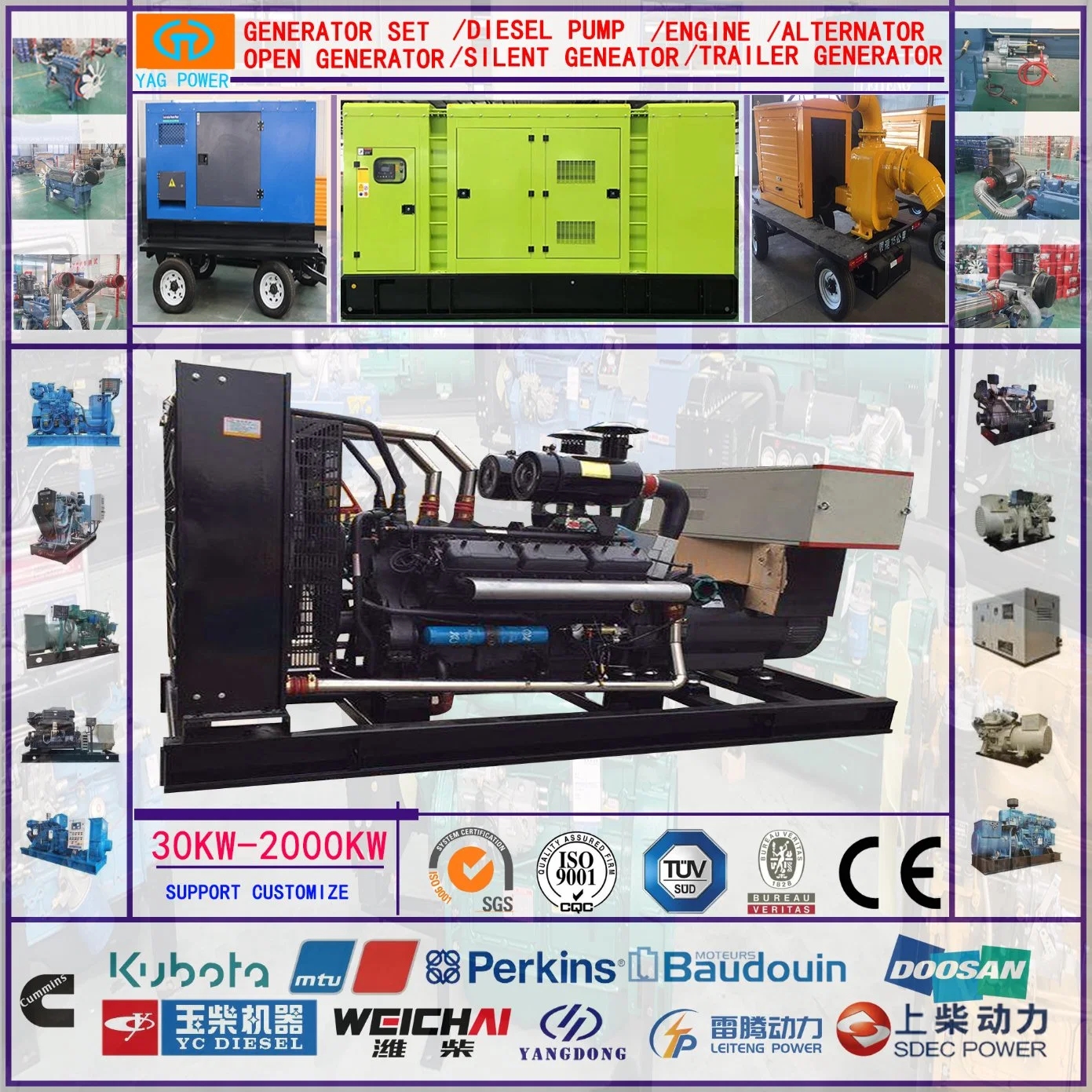
Conclusion
Diesel generators play a vital role in providing backup power for industrial applications, ensuring the continuity of operations during power outages and emergencies. Their reliability, efficiency, and high power output make them a popular choice for industries where uninterrupted power supply is critical. However, the environmental impact of diesel generators, including air pollution, carbon emissions, noise pollution, and spill hazards, must be carefully managed to mitigate their effects on human health and the environment. By implementing proper maintenance practices, fuel management strategies, and compliance with environmental regulations, industrial facilities can maximize the benefits of diesel generators while minimizing their environmental footprint.